Odfjell Drilling
Electrical XMT
Handling System
with Digital Twin
Odfjell Drilling is a leading rig operator driving the oil and gas industry towards more environment-friendly production of oil&gas resources.
Seaonics is a leading technology company specialized in marine lift and handling operations.
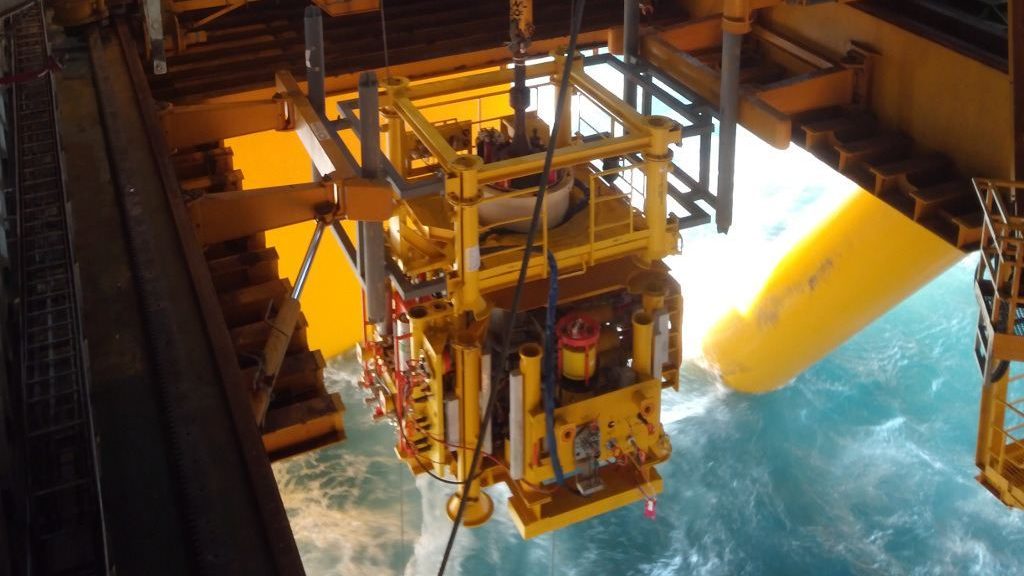
Reliable and custom made XMT handling system
Odfjell Drilling required an electrical handling system for subsea deployment and retrieval of X-mas trees (a special unit connected to the wellhead) for their new drilling platform Nordkapp. The system is used for handling heavy subsea equipment on and in the proximity of subsea well heads. High reliability and safety is an absolute requirement.
Seaonics rose to the challenge and delivered a custom-built all electrical handling system for deployment and retrieval of X-mas trees. The system includes complex control algorithms for active heave compensation (cancelling out the vessel movement relative seabed) and accurate tension control and with advanced function as auto landing. The delivery included multi-level redundancy, a digital twin and a full-scale real-time training simulator.
The system has proven to be highly efficient and has reduced rig downtime with 3-5 days per operation compared to similar operation on other rigs.
The winch solution was designed in close cooperation with Odfjell Drilling and is an upgrade of the single centre rig “Deepsea Nordkapp” to obtain an efficiency closer to the Odfjell dual centre rigs. The winch has a redundant motor system, and has redundant power supply from the rigs power system. This ensure the “safety in compensating” which is required when landing the XMT on the very expensive subsea production wells.
Odfjell Drilling Team
Designed for Industry 4.0 – Maritime 4.0
The solution was developed in the spirit of Industry 4.0 / Maritime 4.0. A digital twin was extensively used during the development and testing of the system. The system has high speed data logging and monitoring, remote access for support and maintenance.
The system integrates IT technology running on industrial servers with industrial automation in a seamlessly distributed system.
The training simulator on board allows the operator to plan and train before any critical operation. Training in critical situations like powerloss/blackout or sensor failures during a critical phase build confidence and comfort to the crew. The combination of a 3D virtual environment built with the Unity3D game engine, the CDP Simulator realtime engine and the built-in CDP control system adds an unmatched experience of reality. Testing out different control algorithms and safety measures reduces time & cost, increases safety and build experience to the team and systems.
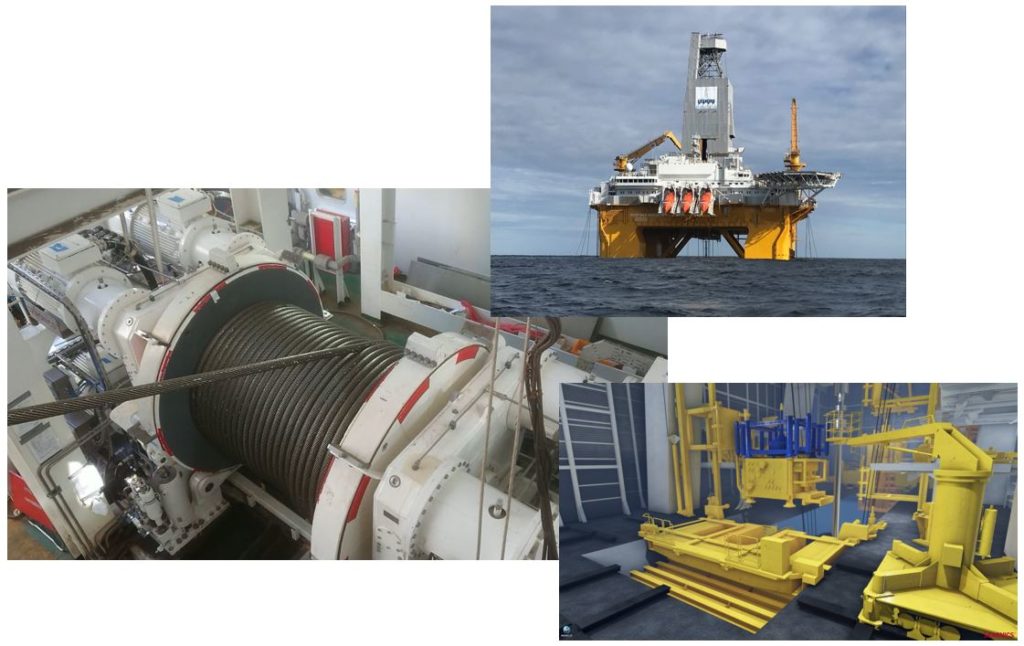
Fast system development using a single tool
The choice to use CDP studio as a preferred development platform reduced Seaonics time-to-market dramatically and allowed for fast delivery to the customer. The system was designed, produced tested and installed in 6 months.
CDP Studio comes with a reliable and tested Framework with a comprehensive toolbox of features. Seaonics has created a set of company feature modules on top of the CDP Framework that contains all their standard building blocks used in multiple projects and products.
The Odfjell XMT system is unique but is built on a reliable Framework and toolbox with tested standard Seaonics function modules. Seaonics developers could therefore focus all their attention and skill on developing the unique features without spending time on setting up the development environment, creating the base system or integrating functions.
CDP Studio is hardware agnostic and comes with cross-platform toolchains and an integrated simulator. The developer could therefore continuously develop and test on their own Windows and Linux PC’s without requiring a test equipment or lab. The digital twin was created step-by-step as developers built the system.
We would never have dared to take on the challenge to develop and deliver a system for critical operations in 6 months without having the field proven redundant core functionality in CDP Studio and the built-in CDP simulator.
Arve Gudmundset
Head of Engineering, SeaonicsThe team could gradually move to the lab with HIL (Hardware In the Loop) testing and with the digital twin. At the end of the development, Seaonics could test the complete system running on the actual target controllers and with a full digital twin simulating the physical equipment. This enables extensive testing of the system and to test various failure situations and emergency procedures.
When installing the control system on the production equipment for FAT testing and commissioning, the control system was already tested, robust and reliable.
Add a Unity 3D gaming engine and graphics to the digital twin and control system and you get a full-scale real-time training simulator.
The tools, methodology and way of work enabled Seaonics to deliver a unique project in record time that is proven to be highly efficient and reliable.
About Odfjell Drilling and Seaonics
Odfjell Drilling: www.odfjelldrilling.com
Odfjell Drilling is a leading rig operator driving the oil and gas industry towards more environment friendly production of oil&gas resources. In order to reduce number of unproductive days for the rig they are constantly taking initiative to reduce wasted energy and money. This can however never compromise safety.
Seaonics: www.seaonics.com
Seaonics is a leading technology company specialized in marine lift and handling operations. Handling loads at sea all over the globe, in Artic and tropical environment , 365 days/year is extremely challenging. Vessels are in motion, there is ice and extreme heat, but the equipment must work.
Talk to us
Do you wonder how CDP Studio can be used in your products or solutions?
Book a demo with one of our team.