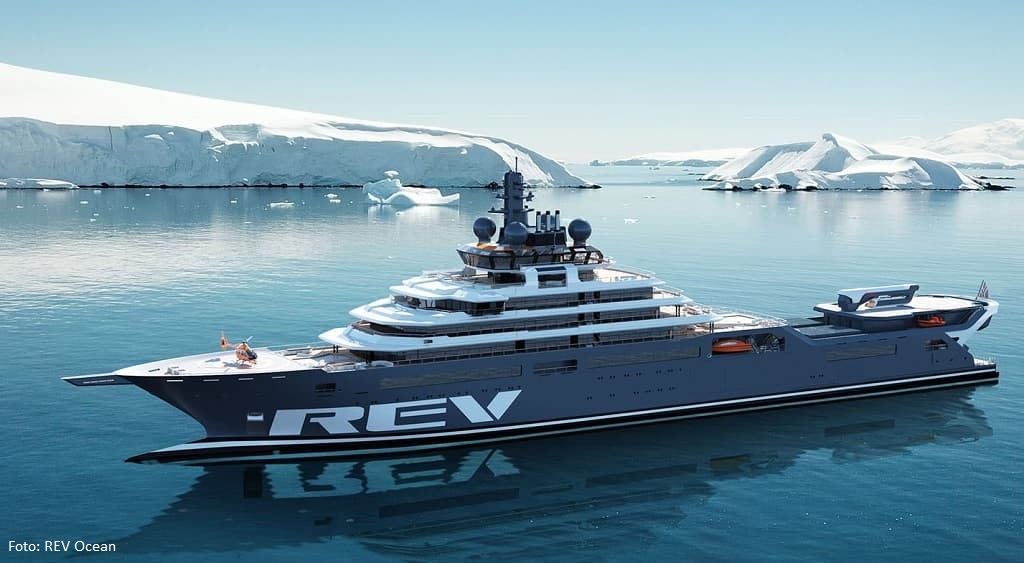
The onshore digitalization wave with Industry 4.0, new technology and market trends are changing the requirements for maritime control systems.
Market trends drives towards green technology, digitalization, improved efficiency, cost reduction, more reliable solutions, safer systems and more focus on life-cycle cost.
Innovation in digitalization is also a way for Western-Europe and US suppliers to sustain and improve their competitiveness when facing lower labour costs and competition from Asia.
The first “Marine 4.0” solutions are entering the market, these are mostly functional additions to existing solutions:
- Performance monitoring
- Condition based monitoring and predictive maintenance
- Remote access and trouble shooting
- Remote controlled operations
Some autonomous operations are becoming available and these are going towards autonomous vessels.
Maritime 4.0 is not only providing upgraded new and innovative solutions but using the new capabilities in the complete product development cycle. This requires the organization to work differently.
The barriers for moving faster towards developing the applications are now often human and organisational:
- Internal resistance from specially the aging workforce in adopting new technology, work methods and processes
- Lack of skills in the workforce and lack of understanding of the benefits new technologies bring
- Unwillingness in standardisation of products and processes
- Limited resources assigned to design and plan the future solutions
Internet of things (IoT), artificial intelligence (AI), data analytics, cloud, big data are important in meeting the new market trends. One challenge is to combine these computer science technologies with traditional automation solutions. Traditional automation systems often use PLC’s and IEC 61131 programming and are not suitable for utilizing these new capabilities.
Electrical XMT Handling System – Odfjell Deepsea Nordkapp platform
Digital twin, simulation, digitalization, green technology, safe and reliable, cost reduction.
A custom-built X-mas tree electrical handling system with active heave compensation was delivered to the Odfjell Deepsea Nordkapp platform. The delivery included a digital twin and a full training simulator. The system is used for handling heavy subsea equipment on and in the proximity of subsea well heads. Safe and reliable operations of the system is of absolute importance.
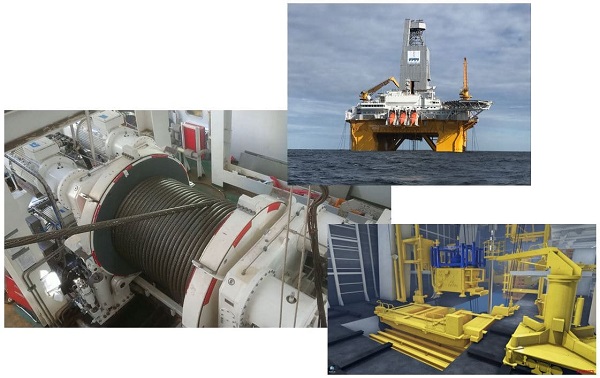
Product vendor benefits
A digital twin was made with the CDP integrated simulator. This allowed the engineers to continuesly test the system during the development, both on their individual computers and HIL (hardware in the loop) with the actual control system. The flexibility saved time during development and ensured a high reliability as different critical situations could be thoroughly tested before delivery.
End customer benefits
The smart design with layers of physical and control system redundancy allows Odfjell to run operation without having other equipment on standby for safety as required on other rigs. The training simulator on board the rig allows the operator to train before any critical operation.
The solution allows Odfjell to conduct operations safer and more efficiently. The all electric system is a greener alternative compared to more traditional hydraulic solutions.
How can modern control system development tools bridge the gap and allow companies to start utilising Maritime 4.0 efficiently?
The competence gap can seem like a huge obstacle as computer science tools are quite different from the purpose-built systems from the automation hardware vendors. This often result in a pushback from the organisation.
CDP Studio is computer science development tool, but specially adapted for developing automation and control systems. It provides a familiar development interface for the PLC engineer whilst it enables the full flexibility and features required for Maritime 4.0 development. The full-blown feature set expected by skilled software engineers is supported.
CDP Studio is therefore very suited to bridge the technology and competence gap enabling companies to start the journey towards Maritime 4.0 applications and development processes.
I.e. for a SME, they only require one engineer able or willing to make high level software code to start the journey towards Maritime 4.0. The rest of the team can continue to use their skill and competence on automation systems in a new tool, but in a familiar environment; thereby alleviating the adoption resistance to new technologies. This also reduces the effort and simplifies the training.
A technical barrier is often to set up a development environment as it is very different from the traditional PLC technologies. CDP Studio comes with the complete development environment out of the box and it is automatically installed and maintained, a feature also appreciated by skilled software engineers.
CDP Studio has inherent properties for supporting the standardisation of products or product building blocks. This allows teams to share these in a controlled manner, reducing development and testing effort at the same time as increasing reliability and quality.
The competence gap is often seen as lack of skills in an automation engineer, but a capable software developer skilled in the computer science domain may struggle to understand automation systems, industrial protocols, industrial IO modules etc. CDP Studio also lower this competence gap as the automation technologies are easily available without detailed technical understanding.
CDP Studio integrates the computer science and automation domains. A computer science engineers can easily use automation technologies and enables automation engineers to utilize the new technologies.
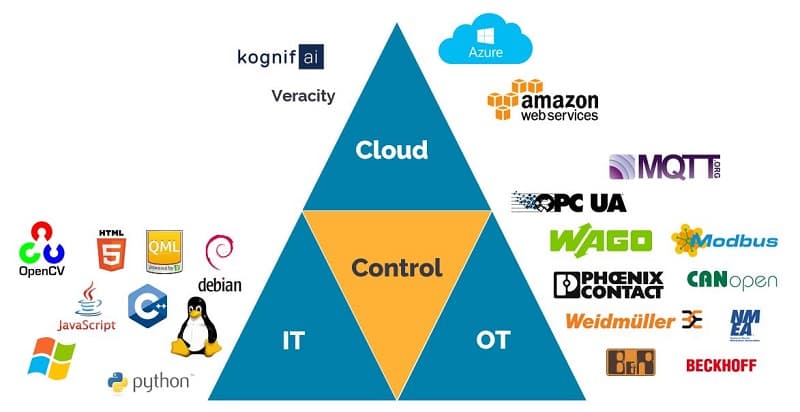
CDP Studio has been used in the marine industry for more than 15 years and is developed to cover the new reality of Industrial Internet of Things, advanced sensors, digital twins, and modern technologies. The below examples demonstrate benefits for the product manufactures and the end customer.
Winches, Cranes and LARS – REV Ocean
Standardization, improved efficiency and cost reduction, green technology.
REV Ocean, a unique exploration and research vessel with a focus to find solutions to environmental challenges and will investigate the entire marine ecosystem. The research equipment includes a LARS (Launch and Recovery System) for UAV, different scientific winches, fishing system and cranes.
Although the systems are unique to REV Ocean, the control system is built by already developed functional modules (high level building blocks) that are tested, and version controlled together with some custom functions. In this way, a unique solution benefit from standardization, thereby achieving cost reduction, faster project execution and a reliable system.
The all electric solution supports REV environmental and green vision.
Autonomous Gangway – Uptime International
Autonomy, digital twin, safe and reliable, Combining computer science with traditional automation.
The active motion control (AMC) gangways are used for personnel and equipment transfer to offshore windmills and oil rigs. The new auto- landing feature increases safety and reduces cost as an operator is not required for the landing or to sit and monitor the operation while the system is in use.
The control system runs on powerful industrial computers for fast calculations, integration of 2D cameras and 3D sensors in combined with standard industrial automation I/O component and instrumentation. Thus, giving both high degree of flexibility and reliability in an advanced, distributed and real-time system.
Digital twins, simulation and HIL test setup like the Odfjell Nordapp rig was used to verify the control system quality and operational safety.
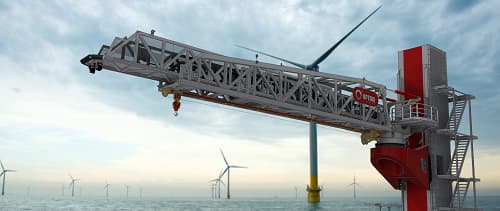
Underwater Drone Docking Station – Blue Logic / Equinor
Improved efficiency, cost reduction, cloud.
The Blue Logic charging station is part of Equinor’s vision to have a network of subsea charging station on the NCS (Norwegian Continental Shelf) to allow autonomous UAVs from any supplier to dock, charge and transfer data. This can give Equinor cost reduction in operating their subsea oil installations and for any UAV operator to compete for the jobs.
A vendor independent development platform allows use of hardware from various vendors, reduces development time and provides a seamless integrated user experience for operational efficiency. The solution combines the control function with a small SCADA system and can ensure that the vendor specific data is transferred to the correct cloud service.
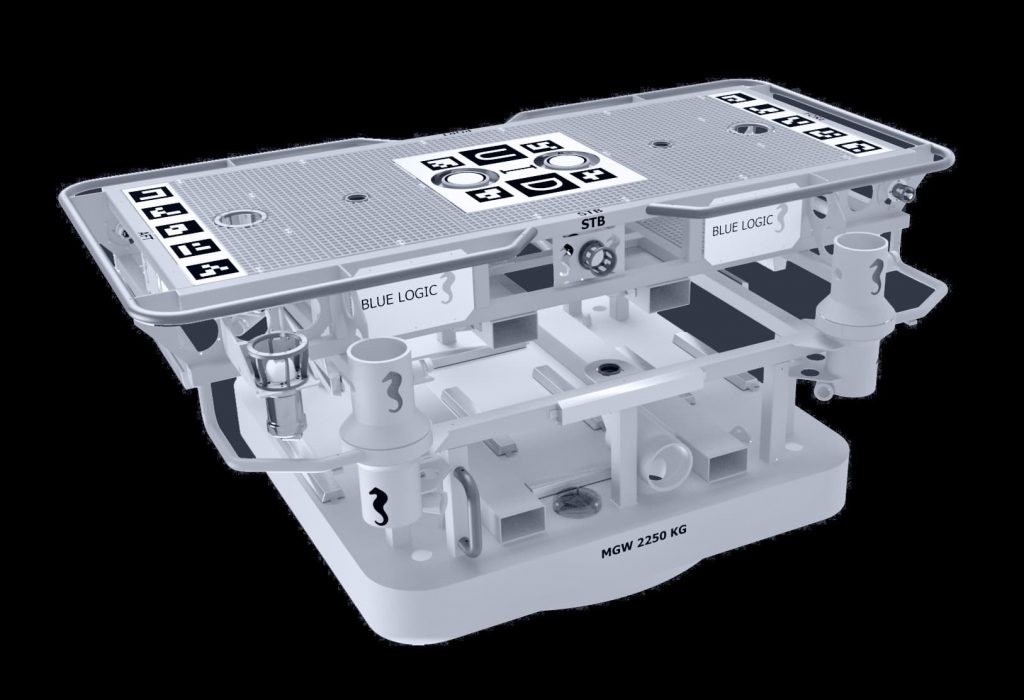
Remote Monitoring and Cloud Connection
Improved efficiency, cost reduction, life-cycle cost, cloud.
The above cases all include the Maritime 4.0 functions as data logging for condition-based maintenance, remote monitoring and support; all are functions important for life-cycle cost. Flexible tools as CDP Studio enables you to collect information from any PLC, computer system or sensor and scales from simple collect and forward solutions to an edge server with local data storage, advanced calculations, provide onboard information to the crew and transfer the right data at the correct time to any cloud service.